As the demand for computing power and data processing speed increases with AI and high-performance computers, the semiconductor industry has also entered the heterogeneous era, where multiple "Chiplets" are widely adopted in packaging.
In this context, the enhancement of signal transmission speed, optimization of power transmission, improvement of design rules, and strengthening of the stability of packaging substrates are particularly crucial. However, the currently widely used organic substrates seem inadequate when facing these challenges, thus seeking higher quality materials to replace organic substrates.
The glass substrate is Intel's answer.
Intel has invested about ten years in glass substrate technology. Last September, Intel announced that it would be the first to introduce glass substrates for next-generation advanced packaging and plans to provide a complete solution to the market in the next few years. This will allow for an increasing number of transistors within a single package, continuing to drive Moore's Law and meeting the computational needs of data-centric applications.
Intel stated that it would use glass substrates for advanced packaging later in this decade. The first products to be processed with glass substrates will be its largest and most profitable products, such as high-end HPC (High-Performance Computing) and AI chips.
Advertisement
So, what are the significant advantages of glass substrates? And how will they play an important role in future development?
01
Why is a glass substrate needed?The demand for substrates originated with early large-scale integrated circuits, as the number of transistors increased, necessitating their connection to a greater number of pins. Over the past 20 years, the primary material used to create substrates has been organic plastic. However, as the number of chips and interconnections within a single package continues to grow, organic substrates are approaching their physical limits.
In this context, ultra-high-density interconnect technologies have emerged in recent years, such as CoWoS and Intel's EMIB technology. These technologies enable companies to bridge critical paths of chips with fast, high-density silicon wafers, but at a considerable cost and without fully addressing the shortcomings of organic substrates.
Against this backdrop, industry companies have begun to explore genuine alternatives to organic substrates, seeking a substrate material that can perfectly integrate with large-scale chips. Although this material may not fully replace CoWoS or EMIB technologies at the highest level of demand, it can offer superior signal transmission performance and denser wiring capabilities compared to existing organic substrates.
How are glass substrates suitable for large chips and advanced packaging?
Firstly, the main component of glass is silicon dioxide, which is more stable at high temperatures. Therefore, glass substrates can more effectively handle higher temperatures while effectively managing the heat dissipation of high-performance chips. This results in chips with excellent thermal and mechanical stability.
Secondly, glass substrates can achieve a higher interconnect density, which is crucial for power transmission and signal routing in the next generation of packaging, significantly enhancing the connectivity of transistors within the chip package. A typical example is Intel's production of system-in-package (SiP) for data centers, featuring dozens of small tiles, with power consumption potentially reaching several kilowatts. Such SiP requires very dense interconnections between small chips while ensuring that the entire package does not warp due to heat during production or use. Glass substrates are the optimal solution currently available.
Lastly, glass is easier to flatten, which makes packaging and photolithography easier, and this is very important for the next generation of SiP. It is reported that the number of vias in glass substrates of the same area is much higher than on organic materials, and the spacing between glass core vias can be less than 100 micrometers, which directly increases the interconnect density between chips by 10 times. Intel sources say that glass substrates can reduce pattern distortion by 50%, thereby increasing the focus depth of photolithography, ensuring more precise and accurate semiconductor manufacturing. Intel anticipates that glass substrates will enable the realization of ultra-large 24x24cm SiPs that accommodate multiple silicon wafers, incorporating more transistors in a single package to achieve greater computing power.Industry Titans Compete to Establish Themselves
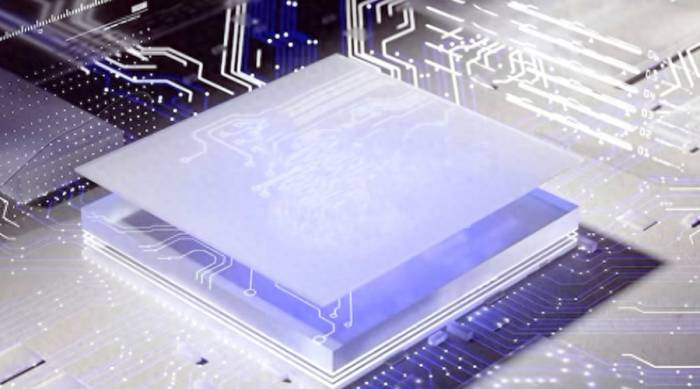
It's not just Intel; in the fierce competition of today's semiconductor field, glass substrates, as a shining new star in the semiconductor industry, are gaining favor from numerous tech giants, including Samsung, LG, and Apple.
Samsung Forms a "Task Force" to Increase R&D Efforts
Recently, according to reports from the South Korean media outlet sedaily, Samsung Group has formed a new cross-departmental alliance. Subsidiaries such as Samsung Electronics, Samsung Display, and Samsung Electro-Mechanics have formed a "unified front" to jointly develop glass substrates and promote their commercialization. It is anticipated that Samsung Electronics will take the lead in combining semiconductor and substrate information, while Samsung Display will be in charge of tasks like glass processing.
Samsung sees glass substrates as the future of chip packaging. At CES 2024 in January, Samsung Electro-Mechanics proposed that a prototype production line for glass substrates will be established this year, with the goal of producing prototypes in 2025 and achieving mass production in 2026.
The formation of a "task force" to increase R&D efforts is a clear indication of Samsung Group's emphasis on glass substrates, and in this technological field, there are already several strong competitors involved.
LG Innotek is Already Preparing
In March of this year, LG Innotek CEO Moon Hyuk-soo stated at the regular shareholders' meeting: "We will develop the semiconductor substrate and electronic system components business to be number one." When answering questions about the development of the semiconductor glass substrate business, Moon Hyuk-soo said: "Our main customer for semiconductor substrates is a large American semiconductor company, which has shown great interest in glass substrates. Of course, we are preparing for this."
AMD Begins Performance Evaluation TestingAMD is conducting performance evaluation tests on glass substrate samples from several major semiconductor substrate companies around the world, and plans to introduce this advanced substrate technology into semiconductor manufacturing. It is reported that the upstream companies participating in this event include Japanese company Shinko Electric, Taiwanese company Xinxing Electronics, Korean company Samsung Electro-Mechanics and Austrian AT&S. The industry predicts that AMD will introduce glass substrates into its products as early as 2025-2026 to enhance the competitiveness of its HPC products. Apple actively explores glass substrates It is reported that Apple is also actively exploring the application of glass substrate technology in chip packaging. The application of glass substrates is not only a material innovation, but also a global technology competition. It is expected to bring revolutionary breakthroughs to chip technology and may become one of the key directions for future chip development. Apple's active participation may accelerate the maturity of glass substrate technology and bring new breakthroughs to the improvement of chip performance. In addition to the field of chip manufacturing, glass substrates are also expected to play an important role in the display manufacturing of consumer electronic products such as smartphones, tablets, and TVs. The replacement speed of these products is accelerating, and the demand for high-quality glass substrates will continue to grow. At present, TSMC is fully committed to the CoWoS field, and has received orders from major manufacturers to enjoy dividends. Therefore, it is not in a hurry to invest heavily in glass substrates, and will continue to upgrade and iterate along the existing path to maintain its leading position. Perhaps when TSMC feels the time is right, it will increase its investment significantly. 03 Mainstream organic substrates in advanced packaging The most commonly used substrates in SiP and advanced packaging include three categories: organic substrates, ceramic substrates, and silicon substrates. Organic substrates are currently the substrates with the highest market share due to their low dielectric constant, low mass density, simple processing technology, high production efficiency and low cost. Organic substrates are developed based on the manufacturing principles and processes of traditional printed circuit boards (PCBs). They are smaller in size and complex in electrical structure, and their manufacturing difficulty is much higher than that of ordinary PCBs.Organic substrates mainly include: rigid organic substrates, flexible organic substrates, and rigid-flexible combined organic substrates.
Rigid organic substrates are made with thermosetting resins as the base material, using inorganic fillers and glass fibers as reinforcing materials. This type of substrate is formed into a laminated sheet through a thermocompression molding process and then combined with copper foil. Rigid organic substrates are suitable for various packaging forms, such as WB-BGA (general chip packaging), FC-BGA (processor and north-south bridge chip packaging), and FC-CSP (smartphone processor and other component packaging), etc.
Flexible organic substrates use PI film with low CTE and high flatness as the dielectric layer, which is combined with copper foil to form the substrate. This type of substrate is widely used in fields such as LED/LCD, touch screens, computer hard drives, optical drive connections, functional components, smartphones, tablets, and wearable devices.
In addition to the two types of substrates mentioned above, some other types of organic substrates are also used in advanced packaging, such as ABF resin, BT resin, and MIS substrates. The choice of these substrate materials depends on specific application requirements, packaging forms, and chip types, among other factors.
At present, the domestication rate of packaging materials and substrates in China is relatively low, and breakthroughs are still needed in the field of advanced substrates. Taiwan, Japan, and South Korea have a higher share in the global packaging substrate market, and the industry competition is relatively stable. Companies in the Taiwan region, such as Xintec Electronics, King Yuan Electronics, Nanya Circuit, and ASE Technology, mainly produce packaging substrates such as WB-CSP, WB-BGA, FC-CSP, and FCBGA.
Looking at the layout of mainland Chinese companies, in recent years, more and more Chinese enterprises are expanding into the packaging substrate field. Mainland China is currently in a rapid expansion phase. High-end FC-BGA substrates can be used for high-performance CPUs and GPUs required in fields such as AI, 5G, and big data. However, the FC-BGA substrate market is currently monopolized by companies such as Xintec Electronics, IBM, and Samsung Electronics. Leading mainland Chinese companies, including Xingsen Technology and Shennan Circuit, are actively deploying in the high-end FC-BGA packaging substrate field in 2023, and it is expected that the production capacity of high-end FC-BGA will be further expanded in the future.
04
Replacing organic substrates?
According to recent research by MarketsandMarkets, the global glass substrate market is expected to grow from $7.1 billion in 2023 to $8.4 billion in 2028, with a compound annual growth rate (CAGR) of 3.5% from 2023 to 2028.Looking at it this way, the market outlook for glass substrates is optimistic, but this track still faces many challenges that cannot be ignored. For instance, the immaturity of technology and the persistently high costs are the two major obstacles in front of the commercialization of glass substrates.
Although glass substrates possess excellent physical properties, such as high flatness and low thermal expansion coefficient, their high hardness and brittleness also increase the difficulty of processing. How to ensure performance while reducing processing difficulty and improving yield is a significant challenge in the production of glass substrates.
In addition, the complex production process of glass substrates requires high-precision craftsmanship and equipment, with extremely high technical demands. At the same time, to maintain a competitive edge, companies need to continuously invest a large amount of R&D funds for technological innovation and product upgrades. This also means that, like any new technology, the production and packaging costs of glass substrates will be more expensive than those of proven organic substrates. This includes the costs of raw materials, processing costs, and subsequent packaging and testing costs. Even Intel has not yet discussed a specific mass production timeline.
As a new entity, the market acceptance of glass substrates still needs to be improved. At the same time, the relevant industry standards and technical specifications are not yet complete, which may affect their promotion and application. In this light, it may take more than a decade for glass substrates to be widely used in commercial applications.
Furthermore, glass substrates and organic substrates each have different characteristics and advantages in their respective application fields, making them more suitable for certain specific use scenarios. Organic substrates are mostly used in the consumer electronics field, while glass substrates are likely to be applied in high-performance computing scenarios. Although glass substrates show potential advantages in some technologies that organic substrates do not possess, organic substrates still have a stable market demand due to their cost-effectiveness and maturity in certain specific applications. Therefore, the two will not completely replace each other but will instead play their respective advantages in their own fields.
05
Driving Glass Through-Hole Technology to Become Popular
Not only is Intel accelerating the development of glass substrate technology, but it also plans to introduce the Glass Through-Hole technology TGV (Through Glass Via), applying a technology similar to Through Silicon Via (TSV) to glass substrates.
Before this, let's briefly understand what TSV is. TSV technology, or Through Silicon Via, is a technique that creates vertical conductive paths between chips and chips, or between wafers and wafers. TSV technology achieves vertical electrical interconnection through the filling of conductive materials such as copper, tungsten, and polycrystalline silicon. This technology is currently the only vertical electrical interconnection technology and is one of the key technologies for achieving 3D advanced packaging.Glass Through-Silicon Vias (TSVs) are vertical electrical interconnections that pass through a glass substrate. As a potential alternative to silicon substrates, they are considered a key technology for the next generation of three-dimensional (3D) integration. Compared to silicon substrates, glass TSV interconnect technology offers several advantages, including excellent high-frequency electrical properties, low cost for large-sized ultra-thin glass substrates, a simple process flow, and strong mechanical stability. It can be applied to 2.5D/3D wafer-level packaging, chip stacking, 3D integration of MEMS sensors and semiconductor devices, radio frequency (RF) components and modules, CMOS image sensors, and automotive RF and camera modules. Based on these benefits, glass TSV 3D interconnect technology has become a hot topic in current advanced packaging research.
Intel's breakthroughs in the field of glass substrates have undoubtedly injected new vitality into the entire industry, while also successfully sparking widespread interest and high expectations within the industry for TSV technology and substrate performance. This breakthrough not only highlights Intel's leading position in technological innovation but also brings new development opportunities for the entire electronics industry.
Comment