On April 3rd, according to statistics from the Taiwan meteorological department, after the main shock, by 10:37 PM on the 3rd, there had been 216 earthquakes with epicenters in Hualien County, Taiwan, and the nearby coastal areas. Regarding the impact of this earthquake on the semiconductor industry chain, the global market research institution TrendForce, also known as the Market Intelligence & Consulting Institute, surveyed the damage and operational status of various factories. The DRAM (Dynamic Random-Access Memory) industry is predominantly concentrated in the northern and central parts of Taiwan, while the Foundry (wafer foundry) industry is spread across the north, central, and southern regions. On the morning of the 3rd, the earthquake in the northern Linkou area was the largest, ranging from 4 to 5 on the Richter scale, with other areas experiencing earthquakes around magnitude 4. Factories have successively conducted shutdown inspections. Although the inspections are not yet complete, no significant equipment damage has been found so far.
The Taiwan region is the world's largest wafer production base. In 2023, it accounts for approximately 46% of the global wafer foundry capacity. Currently, the industry is most concerned about whether the global chip supply will be disrupted and whether the chip shortage situation of 2021 will reoccur.
A single issue can affect the entire system; the challenges for chips this year are not limited to earthquakes, power shortages, and water scarcity...
01
Unsustainability without Water
The production facilities being announced or under construction in the United States and Europe are all located in areas already facing severe water stress. Intel, TSMC, and Samsung are all building new factories in the southwestern United States, which has been in a state of drought since 1994. In 2021, the U.S. Bureau of Reclamation announced for the first time a water shortage in the Colorado River Basin. Future climate change scenarios indicate that over 40% of all new semiconductor manufacturing facilities announced since 2021 will be in watersheds that may experience high or very high risk of water scarcity.
Advertisement
In the context of reducing greenhouse gas emissions that contribute to global warming, the energy-intensive nature of semiconductor manufacturing and its significant carbon footprint have attracted considerable attention. It has been proven that we are both thirsty and hungry. Our industry consumes a vast amount of water, up to 264 billion gallons per year, and with climate change, this resource may become even more scarce. A single wafer fab can use tens of millions of gallons of water per day. From this perspective, the average water usage in the United States is about 310 liters per person per day, and 10 million gallons is equivalent to the daily household water usage of a small city with a population of 122,000.
In short, climate change and water scarcity are posing short-term and long-term risks to semiconductor manufacturing.
Water security will become an increasingly important factor affecting the credit status of semiconductor companies. Improper water resource management can disrupt company operations, damage financial performance, and potentially affect customer relationships. Furthermore, given the integrated nature of the semiconductor supply chain, any potential production disruptions could impact its end markets.Climate change is testing chip manufacturers. As processing technology advances, the absolute water consumption and water consumption per unit of semiconductor companies are both increasing. At the same time, climate change is increasing the incidence of extreme weather, the frequency of droughts, and the variability of precipitation, limiting the ability of chip manufacturers to manage production stability.
S&P Global Ratings believes that water security will become an increasingly important factor affecting the credit status of semiconductor companies. Although most companies have been adept at handling this issue so far, increasingly severe and frequent water shortages could overwhelm the contingency plans of entities.
Driven by capacity expansion and the demand for advanced process technologies, the water consumption of the semiconductor industry is expected to grow at a mid-to-high single-digit percentage annually.
For instance, after TSMC upgraded to the 16-nanometer (nm) process node in 2015, the unit power consumption increased by more than 35%, primarily due to the migration to advanced nodes, which requires more manufacturing processes. There is a direct link between water consumption and chip complexity because fabs use ultrapure water (freshwater processed to an extremely high purity) to rinse wafers between each process. The more advanced the semiconductor, the more process steps there are, and the more water is consumed.
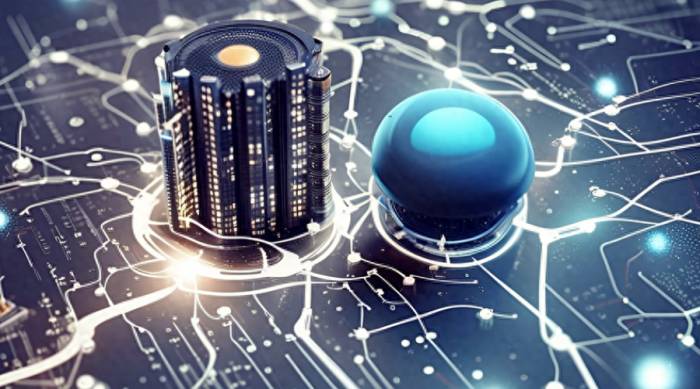
TSMC's water security issues are significant but moderate compared to its peers. Water shortages are not expected to affect the foundry's operations within the next three years; however, beyond that, it's uncertain, as capacity expansion and technology development may leave TSMC with less room to withstand severe droughts. Predictions suggest that by 2030, TSMC's demand for water could double from the 2022 levels.
Take Taiwan as an example:
From October 2020 to June 2021, Taiwan experienced its most severe drought in 56 years. This was due to the absence of typhoons in 2020 and limited rainfall in the spring of 2021, causing reservoir levels to drop below 5% of their capacity. Authorities ordered water restrictions for about two months, affecting over one million households and businesses. The government shut off water supply for two days a week in the most affected areas, including Taichung, Taiwan's second-largest city. A quarter of the island's rice cultivation area was left without irrigation. According to local reports, officials asked the tech industry (especially the semiconductor industry) to reduce water consumption by 20%. Hydropower stations were also disrupted, leading to two major power outages in May 2021.
As the inevitable migration to more advanced semiconductor process technologies continues, the purity requirements for water should also increase. This means that TSMC may have to filter out more water that does not meet its increasingly stringent purity standards. This could limit TSMC's ability to further improve water recycling rates. The global tech hardware supply chain relies solely on a few major chip manufacturers. A reduction in operations at one of these companies could affect the production of many downstream enterprises. The global chip supply shortage during the pandemic has amply demonstrated the complex and event-risk-prone nature of the tech supply chain.Addressing risks Recognizing the need for sustainable development Semiconductor production requires large amounts of water and energy, much of which is treated and discharged as wastewater. As manufacturers seek to scale up production and build new facilities to meet unprecedented levels of demand, it is necessary to remind the industry of the importance of efficient wastewater treatment. Semiconductor manufacturing involves a wide range of complex slurries and chemicals, which require strict wastewater separation, treatment and recycling systems. Dealing with these sludges containing metals and other hazardous wastes is a challenge, and enforcing environmental regulations such as wastewater discharge standards can be costly. The compounds involved in semiconductor production include hydrofluoric acid for cleaning and etching photosensitive components, and ammonia, ammonium fluoride, hydrogen peroxide, and hydrochloric acid, sulfuric acid and phosphoric acid for rinsing. Cleaning semiconductor wafers is the most water-intensive part of the process, generating fluorine-rich wastewater that needs to be neutralized with lime. Solutions for the entire industry chain If an earthquake of magnitude 4 or above occurs somewhere in Taiwan, the first thing chip manufacturers do is evacuate all employees in the clean room and factory and wait for the main earthquake to stop. The next step includes remote monitoring of the factory through a central control system to detect fires, toxic gases or any chemical leaks that could cause serious accidents. If the situation is safe, the equipment, facilities and materials teams can return to the designated site and begin a physical inspection of the equipment. The first step is to determine whether the wafer being processed in the equipment is intact. If so, it can be reworked later. If the wafer is broken, however, engineers need to carefully clean the equipment room and then restart the machine. Next, they run a batch of control wafers to ensure that the machine is operating normally before putting the machine back online. These procedures must be carried out meticulously, and the full resumption of production takes time. An equipment supplier manager said: "It may take from a few hours to a few days or even weeks for all processes to return to normal, depending on the severity of the situation." Industry insiders said that on top of that, all types of lithography machines generally take longer to restart than other chipmaking equipment. "It is always a challenge to recalibrate the deviation of the lithography machine after an earthquake. You need a lot of support from the equipment supplier and use specific tools. It requires extremely high precision, and you can't rush to restore the lithography machine. "This is where the work ethic that Taiwanese engineers are proud of comes in. An equipment engineer said: "If it happens on holidays, or it is not normal office hours, all employees will return to the factory immediately in less than an hour." He also recalled that he once worked non-stop for 48 hours to ensure production efficiency. Ensure that the station he is responsible for resumes normal operation in another incident. "The rapid recovery is also closely related to the work culture of Taiwan's chip industry..."After the earthquake, factory, equipment, and materials engineers as well as suppliers worked overtime during the national holiday to resume production as soon as possible. "We have to conduct many checks and recalibrations. I can assure you that all engineers in the Taiwan region of China are on duty, like wasps swarming out of their nest, helping to get the production tools back online," said a manager.
03
Summarize Experience
Water is becoming more valuable and increasingly scarce. Semiconductor manufacturing requires a large amount of water, primarily for the ultra-pure water needed for the production process itself. Water in the factory also has many other uses: cooling, washing, point-of-use reduction, and firefighting, among others. The amount of water a single factory extracts is equivalent to the water usage of tens of thousands of households, and many wafer fabs are now located in areas with tight water resources.
What can we do? It is necessary to have common measurement standards for the use, reuse, treatment, and recycling of water. Climate change will have a negative impact on water supply in many areas where semiconductor equipment is produced. It is also important to understand the balance between recycling efficiency, energy usage, and carbon footprint. As production increases, innovative approaches involving wafer fabs, local, and national governments are needed to manage this water risk.
Comment