Recently, the news that TSMC has launched a large-scale talent recruitment has attracted a wave of attention.
According to Laura, Senior Vice President of Human Resources at TSMC, the leading semiconductor foundry plans to hire 23,000 new employees in the next few years.
Currently, TSMC's employee count has increased from 56,000 at the end of 2020 to 77,000. Following the aforementioned plan, the company's workforce is expected to grow to 100,000 in the coming years.
So, why is TSMC expanding its workforce on such a large scale? Overall, there are two main reasons: First, globally, it has virtually no competitors in the most advanced processes. Second, it is expanding production lines worldwide, especially in the United States, Japan, and Germany.
01
Demand for 5nm and below advanced process capacity is outstripping supply
At present, the demand for 5nm and below advanced processes from major global IC design companies, represented by AMD, NVIDIA, and MediaTek, is largely concentrated on TSMC. This is particularly true for the 3nm process, where customer demand is growing, necessitating more capacity. Production line construction is ongoing, and over the next two years, as this new capacity comes online, a significant number of wafer fab engineers and technical workers will be required.
Advertisement
In the second half of 2023, Apple's A17 chip will adopt TSMC's 3nm process, and Qualcomm's next-generation processor Snapdragon 8 Gen 3 and MediaTek's Dimensity 9300 will successively use TSMC's N4P process. This year, they will further adopt the N3E process.
TSMC has stated that demand for the N3 process is strong and has seen a significant increase in the second half of 2023. Additionally, the N3E process has been verified and began mass production of the first customer products in the fourth quarter of last year.Following the Snapdragon 8 Gen 3, Qualcomm launched the Snapdragon 8 Gen 4 in March this year. However, most of TSMC's 3nm process capacity is occupied by Apple's chips, with the remaining minority capacity also being allocated to MediaTek. As a result, the Snapdragon 8 Gen 4 can only secure 15% of TSMC's 3nm process capacity. Under these circumstances, due to the improved yield rate of Samsung's 3nm process, Qualcomm will adopt a co-production model with TSMC and Samsung.
Clearly, due to insufficient capacity, Qualcomm's 3nm chips originally destined for TSMC have been diverted to Samsung. Therefore, TSMC must accelerate the expansion of its production capacity and increase the number of employees in order to regain the 3nm process orders within the next two years.
Entering the second half of 2024, more customers' new products will enter TSMC's 3nm process production line, including mobile chips from MediaTek and Qualcomm, as well as server and AI chips from Nvidia, AMD, and Intel.
In recent years, as Intel expands outsourcing, cooperation with TSMC is increasing. It is reported that the CPU based on Intel's next-generation low-power architecture, Lunar Lake MX, will use TSMC's N3B process. It is understood that this project has been initiated within TSMC for quite some time and has accelerated its progress since the end of 2023. At the same time, the CPU based on Arrow Lake H/HX will also use TSMC's 3nm process. In the future, there may be more foundry orders from Intel, and TSMC's production capacity will need to be supplemented.
In the field of high-performance computing chips, Nvidia's H200/H20 and AMD's MI300 are all produced by TSMC, with a large output. Moreover, new products launched this year, especially Nvidia's B100 and B200, will be mass-produced at the end of this year and the beginning of 2025, which will further increase the demand for TSMC's 3nm process capacity.
In addition to the 3nm process, the research and development of the 2nm process technology is progressing as scheduled. TSMC will maintain its industry-leading position in terms of performance, power consumption, and area (PPA), with plans to mass-produce in 2025. By that time, the 2nm production line will require a new team of engineers and technical workers.
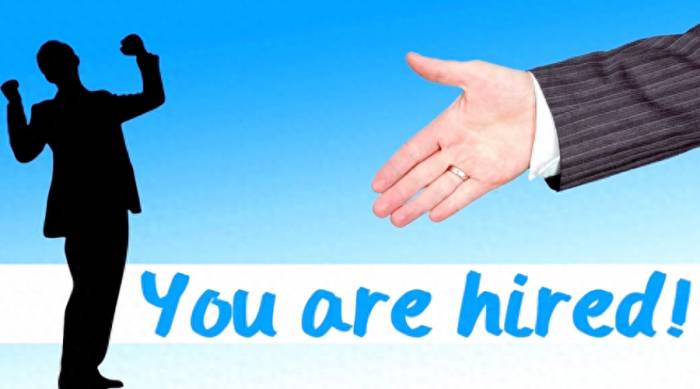
02
Global Expansion of Production Lines, Talent Issues Become Prominent
TSMC is building new wafer fabs in the United States, Japan, and Germany. The company will construct three wafer fabs in Arizona, with the first phase already beginning to move in equipment and expected to produce 4nm process chips by 2025. The second phase of the wafer fab is under construction, with plans to produce 3nm chips, and the third phase has just begun planning. TSMC's Kumamoto factory in Japan is expected to start mass production in 2024, involving processes such as 16nm, 12nm, and 28nm. The German factory has also begun planning, with processes similar to those in the Japanese factory.
TSMC's overseas wafer fab process technology ranges from 28nm to 16nm, 5nm, and the future 3nm, all of which are strategically laid out. The demand for talent in these overseas fabs is increasing. Moreover, the training tasks based on local needs and the Taiwan region are becoming increasingly important. In addition to fab talent, there is also a need to increase the number of employees used for talent training.Regarding the construction of overseas wafer fabs, TSMC said that worker shortages, interruptions in the material supply chain, and construction problems may delay the construction process. Among them, the talent problem of wafer fabs will exist for a long time, and it is necessary to prepare for a rainy day. In the United States, TSMC has two major problems to be solved: one, the progress of the plant review; two, talent shortage. Especially the latter, TSMC originally planned to recruit 4,500 local employees in the United States, but now it faces the fact that American employees are not adapted to the work content, resulting in a delay in recruitment progress. On the American workplace community platform Glassdoor, many Americans who have worked in TSMC's US factories complained that the management did not respect American employees and was unwilling to accept employee suggestions. They even mentioned that "if it is a Taiwanese American employee, he will be envied because he can get more money", and other internal conflicts, which rapidly magnified the management problems of TSMC's US factories. "What I heard is that American engineers are paid better than those in Taiwan," said Chai Huanxin, a special consultant to the Optoelectronics Technology Industry Association. American engineers have higher salaries, do not have to work night shifts, and are even unwilling to obey orders from Taiwanese supervisors. "Americans are used to freedom," this comment points out the difference between American workplace culture and Taiwan. In the American workplace, people are more willing to invest in the software industry with flexible working hours and free corporate culture, while TSMC, which belongs to the manufacturing industry and emphasizes discipline, has difficulty recruiting employees, and the importance of cultivating talents itself is becoming more prominent. In Dresden, Germany, TSMC aims to start building a factory in the second half of 2024 and start production by the end of 2027. Currently, one-third of semiconductor products manufactured in Europe come from Saxony, where Dresden is located. The state has attracted billions of dollars in investment, and wafer fabs of companies such as Infineon, Bosch and GlobalFoundries are located in Saxony. However, a shortage of skilled labor is putting pressure on the semiconductor industry in the region. More than 76,000 people are employed in Saxony’s local chip industry, thanks in part to a nearby cluster of research institutes, semiconductor-related companies and technical universities. However, that number is not enough for Germany, or Europe as a whole.According to a study by IW Koeln, 28% of electrical engineers and 33% of engineering managers in Germany's semiconductor industry will reach retirement age within the next 10 to 12 years. A spokesperson for the German Ministry of Labor stated that the semiconductor industry in Germany was short of 62,000 workers during the period from June 2021 to June 2022. With an aging population and a decrease in Germans entering the workforce, there is still a significant need for a large number of foreign skilled labor.
Silvana Muscella, the technical coordinator of ALLPROS.eu (an EU project funded by the Digital Europe program), stated that in the EU, chip manufacturers struggle to match the salaries offered elsewhere in the world. "Europe is losing talent because they cannot pay as much as Singapore, South Korea, the United States, or Canada."
Broader still, chip manufacturers face difficulties in competing with higher wages offered in other technology sectors, some of which have the added appeal of lower physical demands. Even electrical engineers considering a job change may not prioritize the semiconductor industry; they prefer the software industry.
It would be very difficult, if not impossible, to meet the current and future talent needs of the semiconductor industry solely through Saxony. Only by changing immigration policies can the labor pressure on wafer fabs be alleviated.
In Japan, TSMC would encounter talent issues similar to those in Germany, the specifics of which will not be elaborated here.
03
Countermeasures
TSMC's new 3nm and 2nm process lines in Taiwan, as well as its wafer fabs being built in the United States, Germany, and Japan, all require a significant influx of new talent to ensure the normal operation of the production lines.
In the Taiwan region, there are sufficient software and hardware facilities, as well as a talent training team, which can systematically cultivate the necessary talent for wafer fabs locally. In the United States, Germany, and Japan, in addition to local training, it is also necessary to recruit existing talent from the market and strengthen cooperation with local universities to increase the influence of their wafer fabs in the local industry and market, thereby attracting soon-to-graduate students from related majors to join.
To adapt to the rapidly growing talent demand, TSMC has established a dedicated training factory in Taichung, known as the New Talent Training Center. The center is equipped with 20 machines and 12 teaching measurement and auxiliary devices, offering various on-the-job training without posing risks to production. It is reported that this training process takes about 8 weeks, enabling employees to be ready for work.In the United States, to encourage more technical workers and engineers to be willing to work at its wafer fabs, TSMC is also adjusting to adapt to the American workplace and work culture, trying new management models, such as allowing employees to "work 4 days and rest 3 days," that is, work for 4 consecutive days and then take 3 consecutive days off, as well as not exceeding a 60-hour workweek.
In order to get the new wafer fab up and running as soon as possible, in April 2023, TSMC appointed Wang Yinglang, the former head of the Southern Science Park Fab 14 and once the company's youngest deputy general manager, to the position of CEO of the newly established wafer fab in the United States, to ensure that the factory can quickly get on track.
In Germany, represented by TSMC and Bosch, they have already started, or plan to start, to delve into talent recruitment at universities such as the Dresden University of Technology, as well as research institutions like the Helmholtz Centers and Fraunhofer Institutes, hoping to attract experienced chip experts, young graduates, and skilled workers to join.
Whether in the Taiwan region or in the United States, Germany, TSMC is continuously improving employee benefits, offering not only more attractive salaries (such as starting with a salary higher than the industry average) but also providing various follow-up guarantees (such as housing, children's education, etc.) to increase the stickiness of TSMC to its employees.
According to statistics, the average monthly salary of TSMC employees in Taiwan is four times the basic wage of the Taiwan region. In addition to the routine adjustment of the monthly salary, the most critical part of the annual salary increase for employees is the bonus and the increase in the bonus. According to TSMC statistics, the average salary in 2022 was 3.175 million New Taiwan dollars, a 28.9% increase compared to 2.463 million in 2021, with an annual salary exceeding 3 million, which is rare in the Taiwan region.
After the board's approval, TSMC's dividend distribution in 2022 exceeded 121.4 billion New Taiwan dollars, setting a new record for the total amount.
In 2022, the number of TSMC employees increased to 61,777, an increase of 7,584 compared to 54,193 in 2021. High salaries still have a significant attraction to talent.
04
Impact of Large-Scale Recruitment
In order to ensure the smooth operation of global wafer fabs, TSMC has initiated a large-scale recruitment mode. As the industry leader, such a scale of action in the coming years is bound to have an impact on the industry, especially competitors.First and foremost, as the leader in the semiconductor foundry industry, TSMC's global recruitment of talent is beneficial for enhancing the semiconductor industry's global influence and can attract more young people to join the field.
During the semiconductor boom of the past 3 to 4 years, an increasing number of young people have been paying attention to and joining the industry, with fresh graduates pouring into the sector at levels unseen in other industries. In the United States, a report published by the university recruitment platform Handshake shows that in 2023, the number of job applications submitted to semiconductor companies increased by 79% year-on-year, while applications in other industries only grew by 19%. Among those seeking internships, the interest growth among young workers is particularly high, with a 163% increase in such applications, compared to a 21% increase in other industries.
According to Deloitte, the semiconductor industry urgently needs workers with software and digital skills, with an expected increase of 1 million workers by 2030. Fortunately, more young workers seem eager for such jobs. Christine Cruzvergara, Chief Education Strategy Officer at Handshake, believes that young employees' interest in semiconductors is related to the shift in employee priorities and expectations.
Dana Gharda, University Relations Director at ASML, stated that they feel they are now the "hot cake" in the job market. She observed that among potential employees looking to work in the industry, many have previously held software engineering positions at tech startups.
TSMC's large-scale recruitment will undoubtedly encourage more young people to pay attention to and join the semiconductor industry.
TSMC's actions are a boon to the entire industry, but for competitors within the sector, the situation is not so optimistic.
In the Taiwan region, some companies have indicated that in recent years, TSMC's recruitment boom has led to a significant loss of talent for their companies. For global wafer foundries and IDM companies, facing TSMC's talent recruitment offensive, they have to increase their recruitment costs to some extent, otherwise, all the good employees in the market will be poached.
For TSMC, not only in the Taiwan region, but also in the United States, Germany, and Japan, the company needs to recruit and train a large number of wafer fab engineers and technical workers, which will disperse TSMC's energy and resources.
Comment